In the fast-paced world of printing, where consistency, precision, and high-quality results are essential, the anilox roller plays a crucial role in determining the print's overall quality. Whether you are printing for flexographic, gravure, or offset applications, understanding the role of the anilox roller is fundamental. It is one of the key elements that ensure accurate ink distribution, maintain color consistency, and achieve vibrant prints across various substrates. This article explores how the anilox roller affects your printing process, its significance in achieving optimal print results, and how you can maximize its performance.
What Is an Anilox Roller and How Does It Affect Printing?
An anilox roller is an essential part of the printing press, responsible for transferring a controlled amount of ink from the ink chamber to the printing plate. It features a surface filled with microscopic cells (also called anilox cells) that hold and transfer the ink to the substrate with high precision. These cells come in various sizes and shapes, each designed to store a specific volume of ink, ensuring that the right amount is transferred to the substrate.
The effect of the anilox roller on your printing is profound: it determines the print sharpness, color intensity, and overall print quality. If the anilox roller isn’t calibrated properly, it can lead to ink starvation (too little ink) or ink flooding (too much ink), both of which can cause defects in the print quality.
Key Factors That Affect Ink Transfer on Anilox Rollers
Several factors influence how the ink is transferred from the anilox roller to the printing plate. These include:
Cell Size and Volume: The size and volume of the anilox cells determine how much ink is delivered to the plate. Larger cells hold more ink, while smaller cells provide finer, more detailed ink transfer.
Cell Shape and Pattern: The pattern and shape of the cells also affect how ink is transferred. Laser-engraved anilox rollers typically feature uniform and precise cell patterns, which ensure consistent ink distribution.
Ink Viscosity: Different types of ink—water-based, solvent-based, or UV-curable inks—have different viscosities. Each requires a specific anilox roller with a particular cell volume to achieve optimal transfer without under- or over-saturating the substrate.
Substrate Type: The material you are printing on—whether it’s paper, plastic, film, or metal—can also impact ink transfer. Porous substrates absorb ink more easily, while non-porous substrates require careful control of ink delivery.
By selecting the correct anilox roller with the right configuration, you can optimize ink distribution and ensure high-quality prints every time.
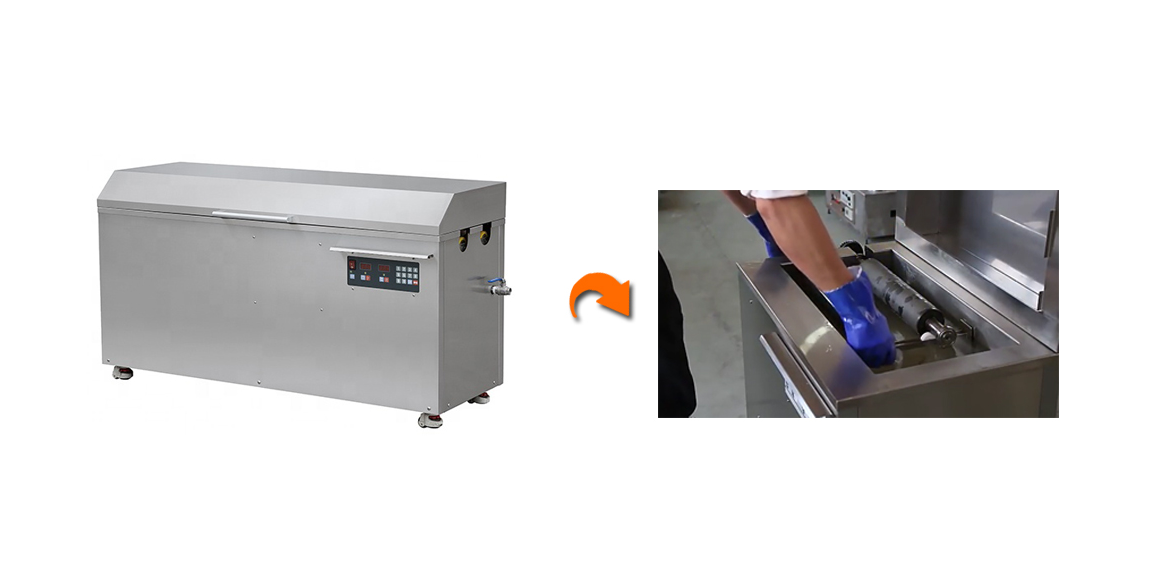
Types of Anilox Rollers: Metal vs. Ceramic
Anilox rollers come in two primary materials: metal and ceramic, each with its advantages and disadvantages. Understanding these differences is crucial in selecting the appropriate roller for your printing needs.
Metal Anilox Rollers
Metal anilox rollers are made from steel or aluminum and are the traditional choice for many printing operations. These rollers are cost-effective and durable but may wear down faster than their ceramic counterparts, especially when exposed to abrasive inks or high-volume production.
Advantages: Affordable, suitable for many applications, and widely available.
Disadvantages: Less durable than ceramic rollers, which may lead to inconsistent ink transfer over time.
Ceramic Anilox Rollers
Ceramic-coated anilox rollers are more resistant to wear and tear than metal rollers. The ceramic coating helps maintain the integrity of the roller's microscopic cells, resulting in longer-lasting performance and more consistent ink transfer. This is especially important for high-end or long-run printing jobs.
Advantages: Longer lifespan, more durable, and consistent performance.
Disadvantages: Higher cost, and may be more fragile than metal rollers during handling.
The decision to choose between metal and ceramic rollers depends on factors like budget, printing volume, and the type of inks used.
Maintaining Anilox Rollers for Optimal Printing Performance
To keep your anilox roller functioning at its best, regular maintenance is essential. Over time, ink residues, dust, and debris can accumulate in the cells, which can impair ink transfer and degrade print quality. Here’s how you can maintain your anilox rollers:
Cleaning Methods for Anilox Rollers
Manual Cleaning: This involves scrubbing the roller using suitable cleaning solvents to remove ink residues. While effective for routine maintenance, this method may not eliminate all contaminants.
Ultrasonic Cleaning: This cleaning method uses sound waves to agitate the cleaning solution, making it more effective at cleaning hard-to-reach areas and removing deep-set ink residue. Ultrasonic cleaning helps maintain cell integrity without causing damage.
Laser Cleaning: Laser cleaning uses a laser to remove contaminants from the roller without affecting the roller's surface. This technique is ideal for ceramic rollers, where cell structure preservation is vital.
Proper Handling and Storage
Handling and storing your anilox rollers properly can extend their lifespan. Avoid scratches, dents, or dings, which can affect the ink transfer. When storing rollers, ensure they are placed in a clean, dry environment and not exposed to moisture, dirt, or chemicals.
The Impact of Anilox Roller Quality on Print Consistency
The quality of the anilox roller directly affects print consistency. A worn-out or improperly maintained roller can lead to inconsistent ink transfer, causing variations in print quality, such as faded colors, blurry text, or uneven coatings. By regularly inspecting the anilox roller for signs of wear and investing in high-quality rollers, you can avoid such issues and ensure the reliability of your print results.
How to Optimize Anilox Roller Performance for Better Results
To achieve the best possible results in your printing jobs, consider these optimization tips:
Match the Roller to Your Ink Type: Ensure the anilox roller you choose has the right cell volume and pattern for the ink type you’re using. For example, water-based inks may require different cell configurations than UV-curable inks.
Monitor Print Quality Regularly: Consistently check for print defects, color variations, or smudging. If any issues arise, inspect the anilox roller for possible buildup or damage.
Schedule Routine Maintenance: Whether it’s manual cleaning, ultrasonic cleaning, or laser cleaning, keeping your rollers well-maintained ensures they continue to perform at their best.
Use High-Quality Rollers: Investing in premium-quality anilox rollers will save you money in the long run by reducing downtime and enhancing print quality.
Conclusion: The Crucial Role of Anilox Rollers in Printing
In summary, anilox rollers are critical components in the printing process, determining the ink transfer efficiency, print consistency, and quality of your prints. Choosing the right anilox roller material (metal vs. ceramic), maintaining it properly, and selecting the correct roller configuration for your specific printing needs can make a significant difference in print quality. By understanding the various factors that affect anilox roller performance and taking proactive steps in its maintenance, you can significantly enhance the efficiency and output of your printing operation.
FAQ
What does the anilox roller do?
The anilox roller controls the amount of ink transferred from the ink chamber to the printing plate, ensuring precise ink application to the substrate.
How do I choose the right anilox roller?
Select the roller based on your substrate type, the viscosity of the ink, and the required print quality. Metal rollers are generally used for cost-sensitive applications, while ceramic rollers are ideal for high-end and long-run jobs.
How often should I clean my anilox roller?
Cleaning frequency depends on usage, ink type, and print quality requirements. Regular cleaning is essential for maintaining optimal ink transfer and roller longevity.