Stacked flexo printing machines are crucial for high-quality printing on flexible substrates like labels, films, and bags. This guide provides a detailed overview of these machines, including their basic principles, operational steps, common issues, and maintenance tips.
Understanding Stacked Flexo Printing Machines
Stacked flexo printing machines feature multiple color stations arranged vertically, which allows for efficient multi-color printing. Unlike other flexo printing machines, stacked models are not suitable for rigid materials such as cartons but excel in printing on flexible substrates.
Key Components:
Photopolymer Plates: Flexible plates that transfer flexographic ink to the substrate.
Anilox Rollers: Rollers that control the amount of ink transferred to the plates.
Drying Systems: Hot air or UV lamps used to dry the ink.
Rewinding Unit: Collects the printed substrate into rolls for further processing.
Steps to Operate a Stacked Flexo Printing Machine
1. Preparation
Before initiating the printing process, the following preparations are essential:
Machine Inspection: Check for wear, damage, and ensure all parts are clean and lubricated.
Plate Setup: Install the photopolymer plates on the plate cylinders for each color station.
Ink Preparation: Mix inks to the required color specifications.
Substrate Loading: Load the substrate material onto the unwinding unit.
2. Printing Process
Here are the steps to follow during the printing process:
Ink Application: Fill the ink reservoirs and ensure the anilox rollers are properly coated.
Printing Adjustments: Set the pressure for each color station to ensure accurate contact between plates and substrate.
Test Print: Conduct a test print to verify alignment, color accuracy, and print quality.
Production Run: Start the full production run once the test print meets the desired standards, continuously monitoring for any issues.
3. Post-Printing
After completing the print run, follow these steps:
Drying: Ensure all printed materials are thoroughly dried before further processing.
Quality Inspection: Check printed materials for defects or inconsistencies.
Machine Cleaning: Clean all machine components, including plates and rollers, to prevent ink buildup.
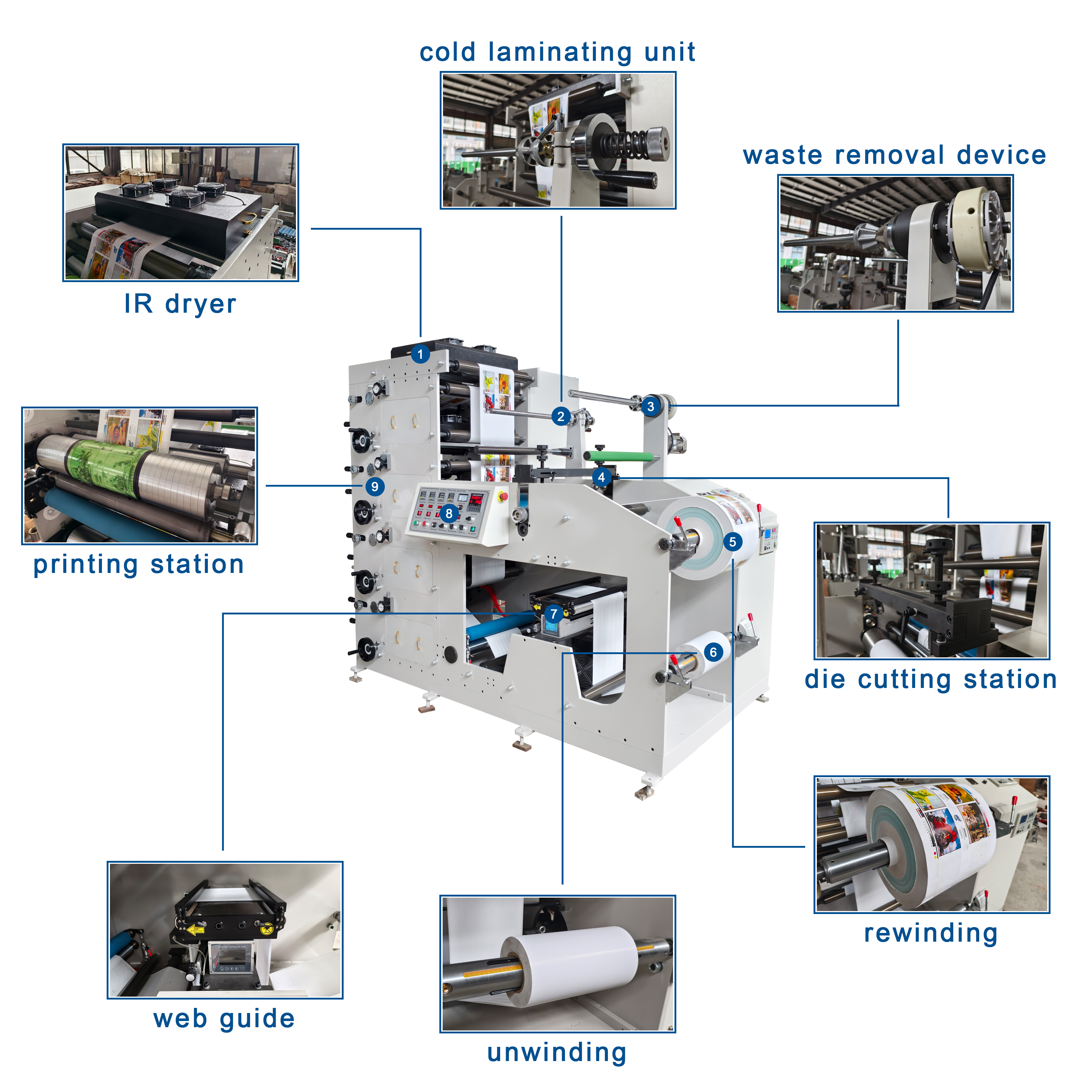
Common Issues and Solutions
1. Ink Spreading
Cause: Incorrect ink viscosity or excessive pressure.
Solution: Adjust ink viscosity and reduce printing pressure.
2. Print Misalignment
Cause: Incorrect plate mounting or substrate feeding issues.
Solution: Realign plates and ensure proper substrate tension.
3. Ink Fading
Cause: Insufficient ink supply or improper drying.
Solution: Check ink levels and ensure appropriate drying settings.
Maintenance Tips for Stacked Flexo Printing Machines
Regular maintenance ensures the longevity and efficiency of your stacked flexo printing machine.
Follow these tips:
Anilox Roller Ultrasonic Cleaning Machine: Clean the machine components after each print run to avoid ink buildup.
Lubrication: Regularly lubricate moving parts to reduce friction and wear.
Inspection: Conduct periodic inspections to detect and address wear or damage early.
Replacement: Replace worn-out parts, such as anilox rollers and doctor blades, as needed.
By adhering to this guide, you can achieve efficient operation, high-quality prints, and extend the lifespan of your stacked flexo printing machine. Whether you are new to flexographic printing or an experienced operator, these practices will help you obtain the best results from your printing projects.